

- #Mach3 cambam endpoint of arc differs how to#
- #Mach3 cambam endpoint of arc differs install#
- #Mach3 cambam endpoint of arc differs update#
- #Mach3 cambam endpoint of arc differs code#
If you do not have SketchUp Pro, you will need to install a plugin to allow you to export in dxf format.


#Mach3 cambam endpoint of arc differs update#
From here, you can modify the original model (which will update changes in the components laid out onto the virtual stock material) in order to occupy the remaining space on the stock material.Īt the end of the CAD process, we export a dxf file that we will import into CamBam. With your model mocked up in 3D, you can create copies of all the components and lay them out flat onto a rectangle the size of the stock material you will be cutting from. This can be useful when designing for lossless manufacturing (manufacturing with near-zero waste product). It will allow you to painlessly select, move, and modify the parts independently from the rest of the model.Ĭomponents in SketchUp are also useful because when you create a copy of a particular component and make a change to one, those changes are automatically updated in all of the clones of that component. Doing so will make your life much easier in the CAD process. Notice that as we are modelling the separate pieces, they are made into components. We will be using 4ft x 8ft sheets of 3/4 inch birch plywood for the main structure material, joined with machine screws and cross dowel nuts. This cart will allow us to store materials and easily move the machine from place to place. In this example, we will be fabricating a cart for our blackTooth laser cutter ( ). So, keep in mind that this tutorial is one of many different ways of going from CAD to final product. You may be using a different CAD program, CAM program, CNC control program, CNC machine, material sizes and fastening methods, and you will likely be fabricating a wide variety of products in the end. Keep in mind during this tutorial that the particular hardware/software tools, materials and application of these instructions will vary from person-to-person, region-to-region, and project-to-project. The tools we will be using are SketchUp for CAD, CamBam for CAM, Mach3 for gcode reading/CNC control, and a CNC router (greenBull from ) for part fabrication.
#Mach3 cambam endpoint of arc differs how to#
Employment Opportunity / RFQ (Request for Quote).This video series shows how to get from CAD, to CAM, to a CNC fabricated product.Thanks for all the help and I'm sure I'll bother each of you again in the future when ever I get stuck. Not only would I not have a working CNC router if it weren't for this site, but I wouldn't be able to get it to do anything useful without this site either.
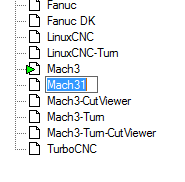
#Mach3 cambam endpoint of arc differs code#
The above code cuts a box with rounded 90 degree corners in CNC Simulator for me and that's exactly the starting point I needed. I know I'll have to change some code on the actual box for a good slip fit between the surfaces, but you all have gotten me over the learning curve.literally I will be learning cutter compensation, which actually is easier for me to understand, but ger21 is right, I need to be comfortable with how each g-code works before I start combining them. Got to love that Louisiana educational system ( Here is what i've got for now. I've got it now! Thanks for all the help folks. If I made any mistakes please correct me. Note: I and J are incremental from the start point even though we are in absolute mode (G90). (the start point of the tool path for the arc is -0.25, +1.5) G01 Y+1.50 (move along Y-axis to start of radius) G01 Z-0.5 (vertical move to cutting plane) G00 X-0.25 Y-0.25 Z+0.1 (move to start point at clearance plane) The lower left corner of the rectangle is 0, 0. The outside cut is 4" in X and 2" in Y with corner radii of 0.5". The X and Y values on the G02 or 3 line define the endpoint, P3, of the arc.Īssume we use G90 (absolute), G40 (no cutter comp), the I-J method, and climb cut. The center point P2 of your arc is Xcenter = P1x+I, and Ycenter = P1y+J. You will start with a straight line to a point P1. Now consider your 90 deg corner and I and J (assuming we are working in the x-y plane). However, the machine will not give an error message for a cutter too large for the intended finished arc. In G40 mode (non-cutter comp) you have to do more analysis for cutter path than in cutter comp mode. In the R method you must have a correct endpoint in relation to the starting point and the radius. In HAAS to cut a complete circle in one operation you must use the I, J, K method. In non-cutter comp you will get the radius of the cutter, and maybe an erroneous cut. In cutter comp you will get an error if this requirement is not met. There can be other limitations on outside cuts. Under some conditions the two radii could be equal. The radius of the arc that you want to generate must be larger than the radius of the cutter.
